Recent News and Updates
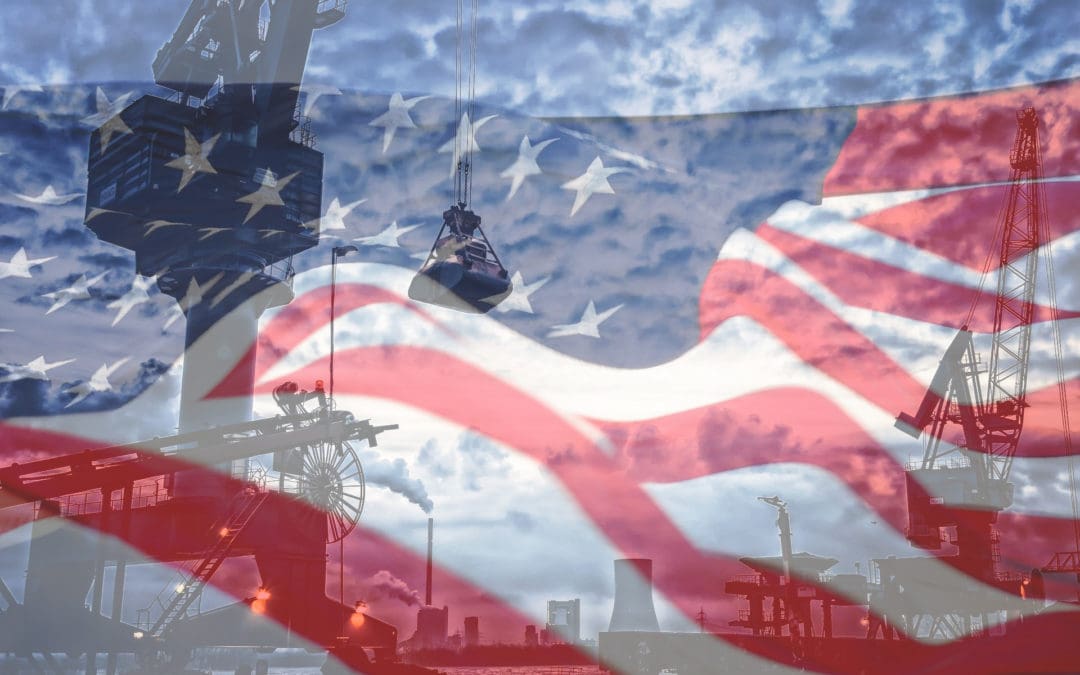
Why American Manufacturers Can Top Outsourcing at Every Turn
Jobs. Something that’s been on everyone’s mind a lot lately. Many are lucky to be able to work remotely, or work for companies that have the ability to guarantee their job until this is all over. However, that’s not the case for a growing portion of the American workforce. This week, UrthPact has been highlighting why manufacturing on American soil is a better option than overseas manufacturing. By sourcing products made in the USA, you are bringing manufacturing jobs back to the US, providing a wide variety of work opportunities to American citizens, and providing your customers with higher-quality, food-safe products.
Jobs began being moved overseas back in the early 90’s and 2000’s. Why? The lower cost of labor allows Asia to make products cheaper. Lower standards of employee support internationally mean that other countries only pay their employees 1/10 of what Americans are paid. As a result, millions of Americans lost manufacturing jobs during this time period. But what have we given up? The availability of critical materials and supplies when demand spikes. The quality of our products. Safe working conditions for employees. Shorter timelines. Successful communication and streamlined development processes. By choosing American-made products, you bring manufacturing jobs back to America, and reap the many benefits of the American workforce.
These benefits elevate and support your company and the US workforce in many ways. Costs of maintaining inventory and shipping are much lower domestically. US facilities and working conditions are certified food-safe and produce products that are approved by the FDA. American prices are competitive with those from overseas manufacturers. And those are just the material things. Due to automation and infrastructure advancements, American manufacturers provide jobs of a much higher quality than those overseas. In 2015, Forbes published an article stating that American workers produce ten to twelve times more output than someone overseas. USA-based manufacturing helps to advance skill sets and encourage ingenuity. As much as American manufacturers benefit from the American workforce, the workforce benefits from the provided opportunities as well.
So why does all of this matter? Because jobs and careers are the backbone of the American economy. And right now, the stress on the economy is on everyone’s minds. Bringing jobs back to American soil will not only benefit the American people and American businesses, but the American economy as a whole. So next time you are deciding whether to purchase a product made in America or made overseas – consider how much better of a product you get when choosing American-made. Consider how much better of an environment it was manufactured in. And most importantly, remember that choosing American-made products not only benefits your company, but America as a nation as well.
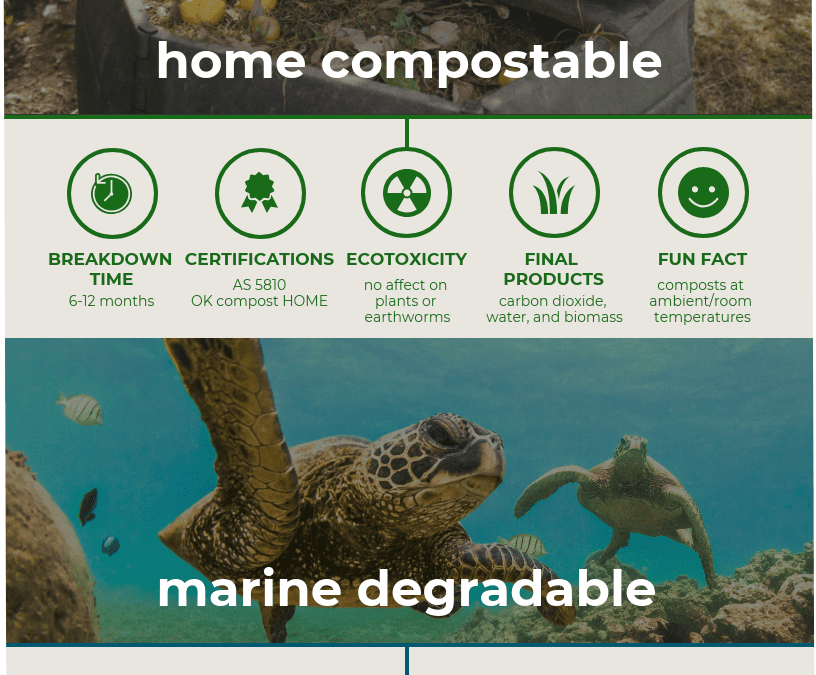
Drinking in the Marine-Degradable and Home Compostable Straw Solution
Today, brands are searching for ways to stand out from the crowd. At the same time, consumers are shopping as much with their conscience as they are with their cash. Brands that can help support causes such as environmental protection can not only attract and retain new businesses; they can also make a difference at the same time. One way that companies can take a leading role and differentiate themselves from the competition is by adopting home-compostable and marine-degradable straws.
Eight million tons of plastic waste flows into oceans annually. One piece of waste that has garnered a lot of media attention is plastic straws. Straws are a huge business in the United States, with an estimated 500 million used daily. Along with plastic bags, plastic straws have become a co-star in a movement of daily things the public can do to help the environment. In some locations, this movement has led to greatly reduced usage and even legal bans on single-use products.
As consumers look to reduce their impact on the planet, they are exploring alternatives to traditional plastic straws including paper, metal, avocado, bamboo, and everything in between. But each of those has its own issues. Paper can get mushy quickly frustrating consumers. Metal straws can alter the taste of the drink and are difficult to clean, and so on. Despite these more traditional alternatives making inroads, many are still searching for something Earth-friendly and consumer-friendly for brands to offer their current customers and attract new ones.
There are innovative alternatives coming to light in home-compostable and marine-degradable bioplastics, that will fill the need of both brands and consumers. These materials maintain the properties of plastic straws but will biodegrade completely in less than a year.
So, what exactly are home-compostable and marine-degradable bioplastic straws? While the science can be a bit daunting, here is a breakdown of how it happens and how it can help the Earth, and your brand.
By Land
Home composting of organic matter such as food and yard waste is familiar to many consumers, especially the growing numbers that are living a more environmentally conscious lifestyle. Compostable bioplastics, in particular, are taking hold and attracting consumers, as they take the planet into consideration while delivering the convenience and consistency of traditional plastics.
Bioplastic products claiming home compostability will completely biodegrade in under a year in any compost environment, whether it’s backyard or industrial. Any product that is compostable should have a stamp of approval from the most widely used international standard called AS 5810 —which defines test methods— paired with TUV’s OK compost HOME, which defines criteria. In a nutshell, [which is compostable too, although slower than many other organic materials] to pass the rigorous and gold-standard certification, the entire two-step process of physical and chemical breakdown needs to be completed in 12 months. The entire process also must occur without negatively affecting plant germination, growth, or earthworms in the ecosystem. Comparably, traditional plastics can take up to 1,000 years to degrade. This process simply breaks them down into smaller and smaller pieces called microplastics, never actually completely degrading, so they continue to impact the ecosystem for a Millenium.
By Sea
Composting works on land. But what about the oceans, where in recent years awareness of plastic waste from straws and other commonly used on-the go-products has skyrocketed, due to its negative impact on marine life? Marine-degradable bioplastics are an up-and-coming technology that will soon be making waves around the world. The certifications for marine degradability are again two-fold: an international standard ASTM D6691 defines testing methods, while TUV’s OK biodegradable MARINE defines criteria. In order to earn their stamps of approval, a material must disintegrate into pieces smaller than 2mm in just 3 months. Unlike a traditional plastic straw that can float in the ocean for centuries, a marine-degradable straw is no longer a threat to marine life a mere 84 days after accidentally entering the ocean. And complete biodegradation to CO2 and biomass takes only 6 months.
Beyond just the physical product itself, it is required that the degradation process has absolutely no impact on at least 90% of test organisms, so there is little to no accidental harm on the ecosystem. In comparison, traditional plastics only break into microplastics, which make up 85% of the plastic waste in our oceans and on our beaches and leach antioxidants, flame retardants, and antimicrobial agents into the oceans, which can also be extremely harmful if ingested by marine life.
Riding the Wave
Home compost in one year vs. microplastics in 1,000 years. Marine degradation in six months vs. microplastics in 500 years. Consumers are searching for these alternatives to avoid stuffing landfills with traditional plastic products. Select companies are already working to bring home-compostable and marine-degradable straws to market in early 2020. And they’re ahead of the curve. The bans on single-use plastics in different areas worldwide have started, and they’re not stopping anytime soon. Plus, there are more consumers looking to make a difference with or without governmental bans, and companies such as Starbucks are joining them in eliminating traditional plastic, single-use straws. This is also a growing and relatively untapped market that brands can capture by offering these eco-friendly straw alternatives.
Consumers are driving change. They are choosing products that won’t only serve their needs, but the Earth’s needs as well. Companies that can provide consumer-friendly and Earth-friendly products will stand out from the crowd while also doing their part to protect the planet.
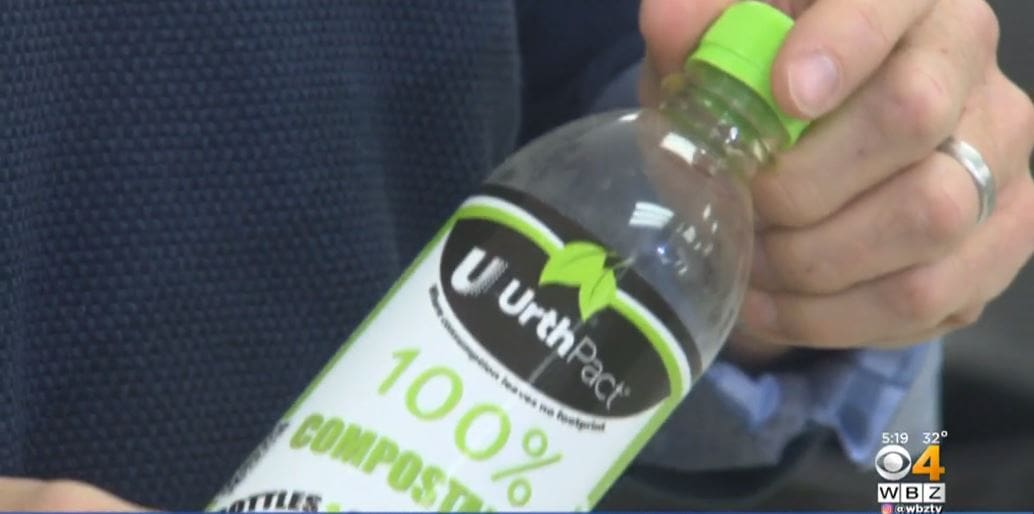
It Happens Here: Leominster’s UrthPact Pioneers New Era Of Bio-Plastics
Leominster, MA — The city of Leominster is known as the “Pioneer Plastics City.” But a shift is happening, and it starts with UrthPact.
“Plastic was invented to be used for Tupperware bowls that would be passed on for generations,” said UrthPact CEO Paul Boudreau. “The mistake we made was we used the same material for products we use for 10 minutes.”
Bio-plastics, or plant based plastics, are the future, he said. And at this local company, everything is compostable.
“The first product we took on was the single use coffee pod,” Boudreau said.
Now, the company produces water bottles, caps and even bio-plastic cutlery, as well as their newest product– the bio-plastic straw.
“If I put this in my backyard in a leaf pile or clippings, two weeks its gone,” Boudreau said of the company’s products.
It’s a straw that’s both good for the planet and good for the consumer, he said. Unlike paper straws, their product doesn’t fall apart, can be tossed after one use and is actually cheaper.
On the warehouse floor, they are pumping out product and can barely keep up with demand.
But they have a singular focus: consumption without leaving a footprint. Pioneering a new era of plastics inside the Pioneer Plastics City, they are changing the game by simply changing the material.
“The plastics pollution problem is solved with bio plastics,” Boudreau said.
There is not much competition in the bio-plastic field yet for UrthPact. Creating bio-plastics is not easy. It is time-consuming and costly. UrthPact hopes the lack of competition has given them a leg up in the field.
The products are only sold to distributors and companies at this point. Consumers will soon start to see their straws at ocean-front resorts and their cutlery at Whole Foods cafes.
Read the original article here.
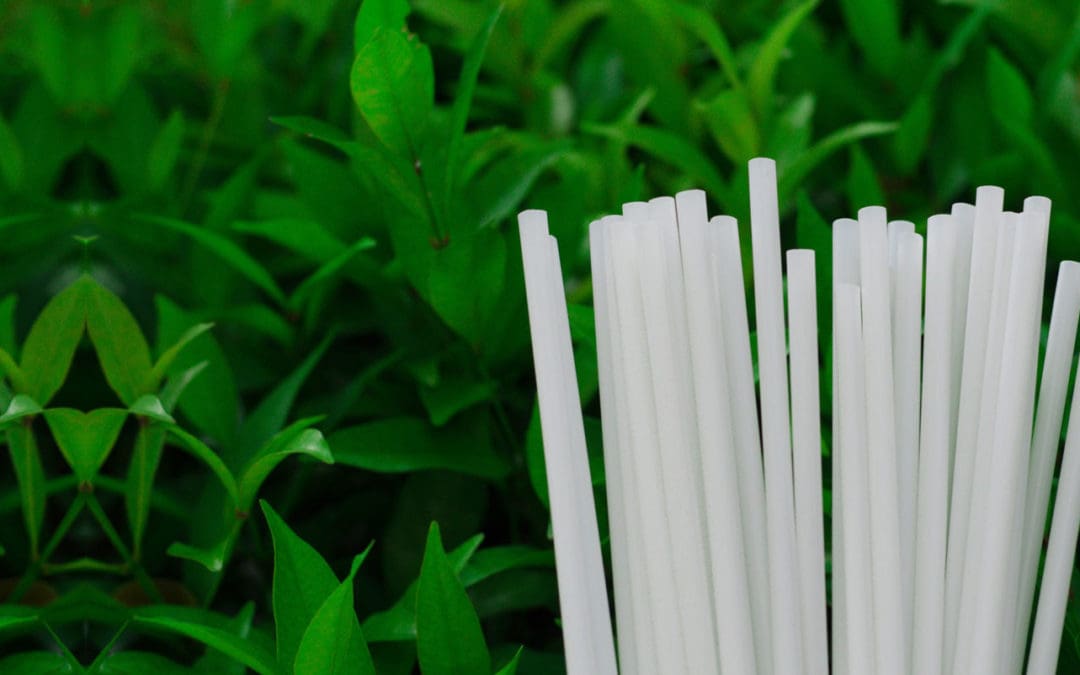
Danimer Scientific and UrthPact to Fight Plastic Pollution with New Compostable Straw
UrthPact expands line of compostable single-use straws with marine degradable options using Danimer Scientific’s Nodax™ PHA material.
Bainbridge, GA — Danimer Scientific, a leading developer and manufacturer of biodegradable plastic materials, and UrthPact, a contract manufacturer of single-use compostable products for leading brands, today announced a partnership to manufacture drinking straws that are fully biodegradable in environments ranging from waste treatment facilities to home compost piles, waterways and our oceans. The products produced through this partnership will help reduce the environmental impact of the estimated 8 million tons of plastic waste that leak into oceans every year.
Single-use straws certified for industrial composting are available now for purchase from UrthPact, with straws certified for home composting and marine degradation to begin shipping in the first quarter of 2020. UrthPact is currently evaluating interested distributors and brand owners to partner with for the sale of these biodegradable straws. The straws are manufactured using Danimer Scientific’s signature biopolymer, Nodax™ polyhydroxyalkanoate (PHA). The plant-based material was verified as an effective biodegradable alternative to traditional petrochemical plastics in a 2018 study led by University of Georgia (UGA) researchers and members of the UGA New Materials Institute.
“Reducing the environmental impacts of single-use plastics is a critical issue that will get worse the longer it goes unaddressed, so it has been encouraging to see industry leaders swiftly collaborate on solutions,” said Stephen Croskrey, CEO of Danimer Scientific. “Since developing a prototype for the first fully biodegradable plastic straw last year, our team has worked diligently with UrthPact to make it commercially available. We look forward to continuing our longstanding partnership with UrthPact in bringing more eco-friendly plastic packaging to manufacturers in the years to come.”
UrthPact, a United States manufacturer, produces straws in its Safe Quality Foods (SQF) certified plants alongside a wide range of compostable single-use plastic products, including coffee pods, valves, cutlery, bottles, caps and more.
“Cities and businesses are exploring outright bans of single-use plastic straws. This may not be a viable option for every business segment within the global market,” said Paul Boudreau, CEO of UrthPact. “One ideal solution is a single-use straw that offers the durability and reliability of traditional plastic without the environmental impact that it can leave upon disposal. With the support of Danimer Scientific, we’re making that ideal a reality.”
Danimer Scientific’s Nodax™ PHA possesses seven TUV AUSTRIA certifications and statements of industrial and home compostability, is biodegradable in anaerobic soil, freshwater and marine environments and is 100% bio-based. All of Danimer Scientific’s biopolymers, including its Nodax™ PHA, are FDA approved for food contact.
Read the original press release here.
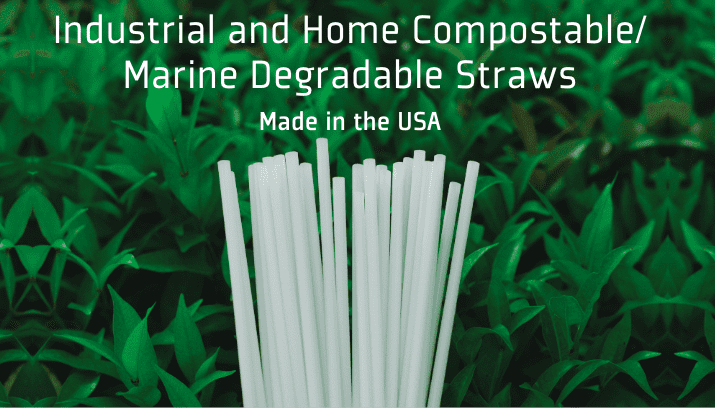
Sip on This! American Manufacturer Releases Compostable Straw Line
UrthPact leading the way to a more sustainable future with its newest single-use product line.
Leominster, MA, April 22, 2019, Nestled within a generation of consumers concerned for the future of our planet, UrthPact, a US manufacturer of compostable products that are typically produced using petroleum plastics, is pleased to announce its expansion to a new line of plant-based straws. Already a worldwide industry leader in compostable coffee pods, one-way degassing valves, cutlery and bottles and caps, UrthPact is once again flipping the single-use product world upside down with its continued innovation and earth-friendly objectives.
Produced in the US at both their East and West Coast facilities, the first in a two-product line-up includes Industrial Compostable straws, which are available now. The second-tier of the line, slated to hit the market in January of 2020, raises the environmental standards even higher with a Home Compostable/Marine Degradable option.
When given the choice between comparable products that are either compostable or will sit on the earth for hundreds of years, most people will choose the sustainable option. The problem with many of the items developed recently, is that they do not function as well as their petroleum-based counterparts. This sub-par performance has particularly been the case with the sustainable straws produced to-date.
Paul Boudreau, CEO of UrthPact explains, “We realized that people are unhappy with today’s alternative for earth-friendly straws,” which is why the company decided there was a need to produce an upgraded version. “Our straws function like traditional plastic straws, but are safer for the environment,” he continued. Boudreau hopes that with this new alternative more businesses will be willing to switch to this sustainable option, eliminating customer complaints and creating an all-around win for the corporate, consumer and natural worlds.
With all-of-the-above to consider, why not just eliminate straws all-together? “Perhaps someday straws will be a thing of the past, but for now they are so embedded into our culture, businesses will continue to use them. At least now we have a better option to offer,” said Boudreau. He also noted the need to respect the many members of our ADA (Americans with Disabilities) community who rely on the use of straws to help with everyday functionality.
A History Lesson… Not the First, But the Best Bet
UrthPact’s East Coast plant is located in Leominster, Massachusetts, known as the Pioneer Plastics City for claiming the invention of the plastics industry we know today. Now with UrthPact’s growing presence, a new sustainable revolution is taking place. “What began ten years ago with the development of a compostable golf tee is exploding in all directions,” notes Boudreau. “People want to see more earth-friendly options and we have the ability to create and supply those items.” UrthPact also manufactures out of Lincoln, California, creating a coast-to-coast catalogue of product availability.
Boudreau recognizes UrthPact is not the first to tackle compostable straws but explains the benefits of using a US-based company, “Straws and other items manufactured overseas may not have the same quality standards that we have in the US.” UrthPact’s compostable items are produced in its SQF (Safe Quality Food) certified plants, guaranteeing safety.
Additionally, the shipping requirements to import products from overseas only increase their total carbon footprint. “That’s like solving one problem but creating another,” remarked Boudreau. “Being able to manufacture on both sides of the country allows for fast and easy shipping to all locations within North America without the added stress on the environment.”
Next Big Dive for UrthPact… Into the Ocean
UrthPact has been going green for years but is now shifting its attention to going blue. Despite clean-up efforts throughout our oceans, petroleum-based plastics, unless eliminated, will continue to haunt our waterways and the ocean life that inhabit it. “It’s one thing to save the land we stand on,” pushed Boudreau, “but our planet is far more blue than green. It’s time to clean up our act in the oceans.”
Which is why coming in January of 2020, UrthPact aims even higher with its first shipments of Home Compostable (AS-5800) and Marine Degradable (ASTM-D6691) straws. Compared with Industrial Compostable straws (ASTM-D6400), which require specialized facilities to fully break down, this version will rapidly return to nutrient-rich soil in a home garden composter or biodegrade in a marine environment. “Should these straws make it into the ocean, they will completely biodegrade, taking us one step closer to cleaner oceans,” declares Boudreau.
Boudreau is sharing the results to the independent lab testing work they have done and is looking to work with marine biologists throughout this process. “We will only make claims that are supported by science and are accepted by the people out there who care the most for our oceans,” Boudreau states. “We may not have the final solution to this big problem just yet,” he exclaimed, “but while we work towards that, we believe we have created something that will stop the damage being done right now.”
Taking Orders Now
UrthPact’s Industrial Compostable straws are now available for purchase. Customers can also pre-order home compostable/marine degradable straws for delivery in January 2020, but quantities will be limited. Those currently ordering Industrial Compostable straws will have first access to their home/marine line.
For more information on the above or UrthPact’s other endeavors, please visit: www.urthpact.com or contact Lauren MacKay at 978-847-9747 or lmackay@urthpact.com
“UrthPact helps brands create products and packaging from earth-friendly materials, protecting a world that needs it and championing a generation of consumers that demand it.”
Read the original press release here.
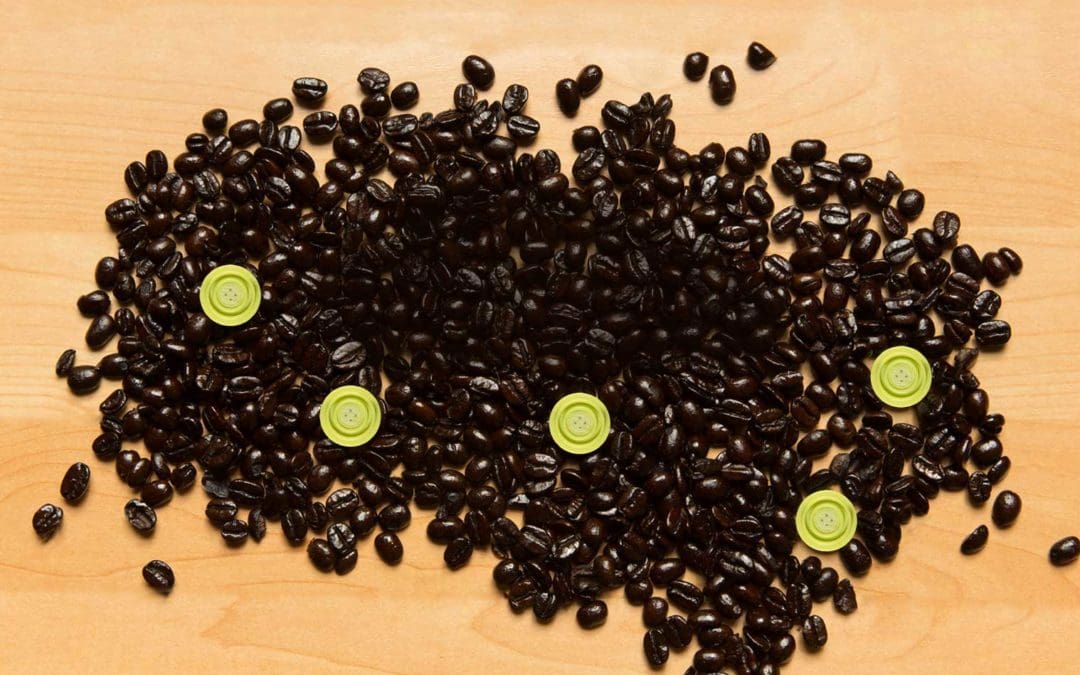
Elevate Your Coffee Packaging with One-Way Degassing Valves from evalv®
As the amount of discarded plastics in our environment grows, the pressure to provide eco-friendly packaging options has rightfully increased. For environmentally conscious coffee producers, there has been one particularly stubborn packaging element that simply refused to change with the times. Compostable coffee bag film solutions are not able to be used with a polyethylene valve. The evalv® opens the door to using a fully compostable bag.
With evalv®, Eco-Friendly Coffee Packaging Is 100% Compostable
The experts at UrthPact sought to create an environmentally safe solution. Developing a sturdy, multi-component valve assembly from compostable plastics is a significant technical challenge. However, as the leading experts in injection-molded compostable bioplastics, our engineers were uniquely suited to solve the problem.
The result is evalv®, a 100% compostable degassing valve that fits easily into most existing valve applicators. evalv® looks and performs just like conventional coffee valves—the only difference is the material. They are made with bioplastics sourced from canola seeds or cornstarch; they meet the ASTM and ISO standards for compostable materials. In commercial composting environments in as little as three months, evalv® will fully break down into compost. When paired with a compostable plastic bag, the entire package can be easily composted both commercially and domestically.
evalv® Can Do More Than Coffee
Compostable, one-way degassing valves are not just limited to packaging for coffee beans. Many packaging applications that utilize degassing valves—from fertilizer to sauerkraut—can be made more eco-friendly with evalv®. Any fermented product packaged with one-way degassing valves can also be packaged using evalv®.
If you’re interested in making your coffee packaging completely compostable and eco-friendly, contact UrthPact today.
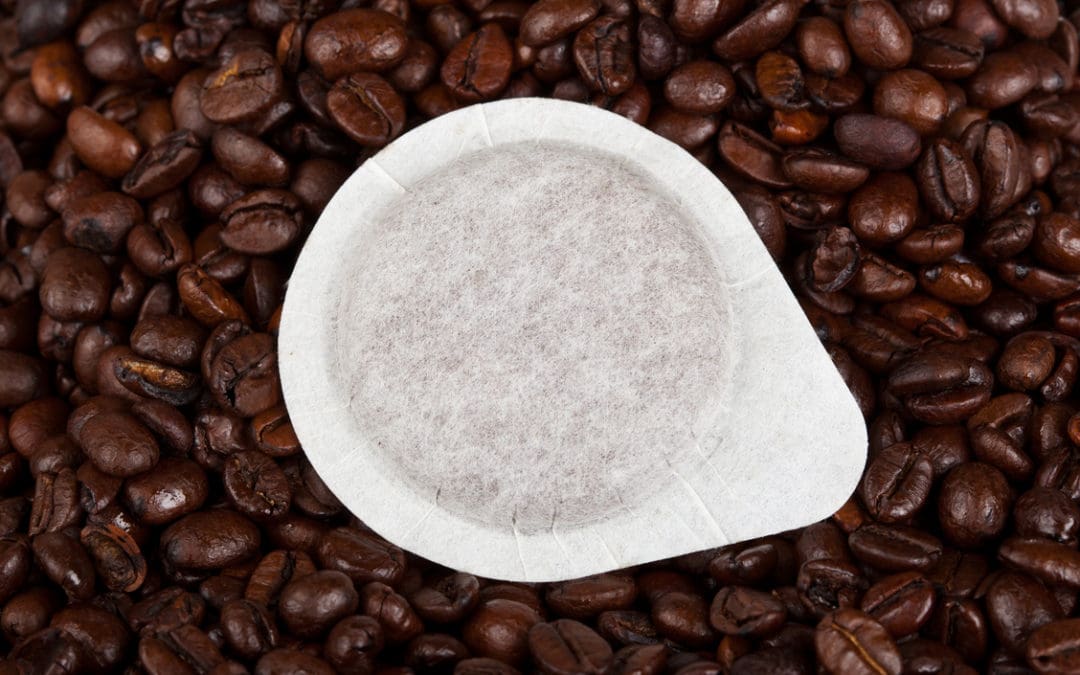
The Basics of Bioplastics
It’s no secret: Plastics are a major threat to our environment. The United States alone generates over 30 million tons of plastic waste each year, with only 10% of that figure being recycled. The rest is piled into landfills or left to scatter across the globe, where it can take more than 500 years to break down. Every piece of plastic made within the last century is still present somewhere on Earth—and that’s a big problem.
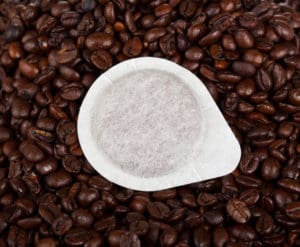
UrthPact produces compostable plastic rings for single-use coffee pods.
The development of biobased plastics, or bioplastics, has provided humanity with a more eco-friendly alternative for the production of packaging and single-use items. The industry is steadily growing; market experts predict global bioplastic production capacity will increase from about 2.05 million tons globally in 2017 to approximately 2.44 million tons in 2022. In theory, bioplastics could replace any disposable item made from plastic, such as cutlery, packaging, and straws.
There is currently a wide range of bioplastic types with specific end-of-life options for each variety. Some biobased plastics can be composted, while others must be recycled. Some are “biodegradable” while others break down almost as slowly as traditional plastics. Understanding which biobased material is best for your product can be confusing. So we’ve put together this guide to help you learn the basics of bioplastics.
What Are Bioplastics?
By definition, the term bioplastic can be applied to any plastic material that is primarily derived from renewable organic materials, such as corn starch. Other biomass sources include milk, tapioca, and vegetable fats. Unlike conventional plastics—which are made through the distillation and polymerization of non-renewable petroleum reserves—bioplastics present us with ecological advantages that can help reduce pollution of natural ecosystems and shrink our energy footprint.
Types of Bioplastics
When we refer to bioplastics, we’re addressing a large category of biobased polymers with a variety of unique attributes and applications. The list is always expanding as new materials are discovered. The most common bio-based plastics include:
- Starch-Based Bioplastics: Simple bioplastic derived from corn starch. They are often mixed with biodegradable polyesters.
- Cellulose-Based Bioplastics: Produced using cellulose esters and cellulose derivatives.
- Protein-Based Bioplastics: Produced using protein sources such as wheat gluten, casein, and milk.
- Aliphatic Polyesters: A collection of biobased polyesters including PHB (poly-3-hydroxybutyrate), PHA (polyhydroxyalkanoates), PHV (polyhydroxyvalerate), polyhydroxyhexanoate PHH, PLA (polylactic acid), polyamide 11 (PA11). They are all more or less sensitive to hydrolytic degradation and can be mixed with other compounds.
- Organic Polyethylene: Polyethylene that has been produced from the fermentation of raw agricultural materials like sugar cane and corn, rather than fossil fuels.
Are All Bioplastics Compostable?
It seems like the answer to this question should be a resounding “Yes!” After all, it would be easy to assume that anything “biobased” is inherently compostable. However, this is simply not the case.
The term biodegrade refers to the process by which microbes break down a material under suitable conditions. Technically speaking, all materials are degradable but we typically only refer to those that degrade within a relatively short period of time (less than a year) as “biodegradable”. Because of this, not all bioplastics are considered biodegradable. In fact, bioplastics fall within a few different categories based on their applicable end-of-life solution.
- Degradable: All plastics, including traditional petroleum-based plastics, are technically degradable. Given the right amount of time and environmental conditions, they will break down into tiny fragments. However, the materials used to make traditional plastics will never fully return to a “natural” state and will continue to pollute the environment with chemical compounds.
- Biodegradable: Unfortunately, the term biodegradable has proven to be problematic because it often lacks clear information about the process requirements and timeframe required for biodegradation. In fact, to prevent consumers from being misled, California actually banned the use of the word biodegradable for any plastics sold within the state. Bioplastics that are considered “biodegradable” can be broken down by microorganisms such as bacteria, fungi, and algae into water, carbon dioxide, methane, biomass, and inorganic compounds. For practical purposes, bioplastics that can be completely broken down within a few months are considered biodegradable. Bioplastics that biodegrade more slowly (requiring up to a few years to be broken down) are referred to as “durable.”
- Compostable: Compostable bioplastics can be broken down by microorganisms into nutrient-rich biomass in as little as three months and leave behind no toxins or residue. Some compostable bioplastics require high temperatures to decompose and must be returned to commercial composting facilities, while others can be composted in home gardens. Polylactic acid (PLA) is a compostable, injection-molded bioplastic that is quickly replacing petroleum-based polymers for the production of food packaging and single-use items because it can be easily composted. PLA also produces 70% fewer greenhouse gases when it degrades in landfills. To be considered compostable, bioplastics must meet the ASTM D6400 standard for compostability.
Where Are Bioplastics Currently Being Used?
Bioplastics might sound like a new-age concept, but in fact they have existed for one hundred years, at least. The Ford Model T, for example, was produced using parts made from corn oil and soybean oil. As the problems surrounding petroleum-based plastics have become more apparent, bioplastics are more frequently used to make food containers, grocery bags, disposable cutlery, packaging, and more. PLA in particular has been used for a wide array of applications, including plastic films, bottles, medical devices, and shrink wrap. It has also been used for specialized applications in 3D printing. Many major companies—including Coca-Cola, PepsiCo., Heinz, Ford, Mercedes, and Toyota—have adopted bioplastics in their packaging materials.
How Can I Make My Products More Eco-Friendly?
At UrthPact, our goal is to help our customers produce eco-friendly products that won’t contribute to the global plastic problem. We specialize in injection-molded bioplastics, made in the USA, that can be easily composted by consumers. It is our mission to create positive contributions to an upward trend in environmentally friendly product use and waste management.
According to the EPA, the amount of waste diverted from landfills through proper composting methods has quadrupled since 1990. Producing single-use products from compostable bioplastics will bring that number even higher. For example, industrial food composting sites have to diligently screen food debris for petroleum-based plastic cutlery. Compostable cutlery would eliminate this problem. In addition, the production of compostable bioplastics requires one-third of the energy required to make petroleum-based plastics.
Compostable bioplastics have the potential to help solve the environmental issues surrounding our love of single-use plastic products. To find out more about how UrthPact can help you make the change to eco-friendly bioplastics, contact us today.
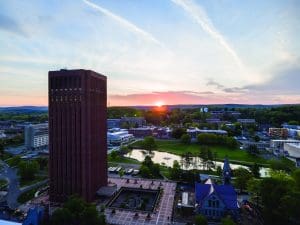
Recycling and Composting at UMass Amherst: Getting Smarter About Waste
Colleges and universities have always been a wellspring for innovation and the University of Massachusetts Amherst has been a stand-out among them. As social and economic concern has grown over how we manufacture, consume, and discard products, UMass Amherst has brought its intellectual and educational firepower to bear on issues such as recycling, composting, and sustainability.
It all began in 2007 when the president of the five-campus UMass system signed the American College and University Presidents’ Climate Commitment. In response, UMass Amherst established an Environmental Performance Advisory Committee (EPAC) that developed the campus’ first Climate Action Plan, which was released in 2010. Two years later, the plan was revised by the Chancellor’s Sustainability Committee, formerly EPAC. The revised plan reflected campus accomplishments and presented a comprehensive blueprint for future sustainability efforts across all aspects of the campus. Climate Action Plan 2.0 helped establish metrics and sustainable goals for the campus.
Subsequently, undergraduates and graduate students campaigned to encourage a more environmentally friendly and ecologically sound approach to campus operations, including the hiring of Ezra Small as the school’s first Campus Sustainability Manager in Facilities & Campus Services. Today are more than a dozen employees focused on sustainability and working in a variety of positions, including, their communications, residential life, the library, and physical plant operations.
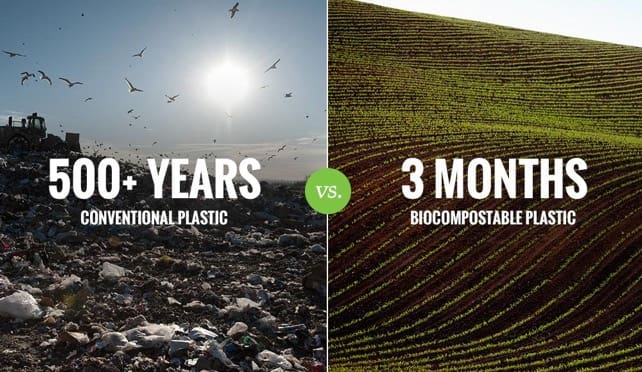
Industrial Composting: What It Is and How It Works
The world is awash in traditional, petroleum-based plastics that are choking our waterways and filling up our landfills. Here at UrthPact, we’re committed to compostable plastic products, providing manufacturers and consumers with the plastics they want and need, but created using environmentally-friendly, biodegradable raw materials that can be safely composted to nourish the earth.
Today, in addition to the conventional backyard compost pile or bin that can efficiently handle small amounts of waste materials from lawns, gardens and kitchens there are industrial composting facilities designed to effectively process large volumes of municipal and commercial waste.
There are basically three techniques used in industrial composting: windrow, in-vessel, and aerated static pile composting. Windrow composting is an open-air process that places the composting material into long piles approximately 5 feet high called “windrows.” These windrows are turned regularly to ensure that all the composting materials spends some time in the warm, moist center of the pile where bacterial activity produces heat that encourages further breakdown. Because windrow composting is on open air process, it is used primarily for yard and garden waste to help control odor.
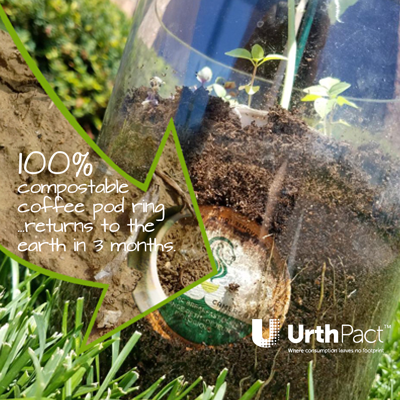
Bioplastic Manufacturing
What is Bioplastic Manufacturing?
Bioplastic manufacturing is the next-generation solution for manufacturing inexpensive, durable, attractive plastic products that are more earth-friendly and environmentally-safe than traditional petrochemical-based plastics.
Bioplastic manufacturing uses renewable biomass sources such as plant-based feedstocks including corn, rice, palm fiber, potatoes, wood cellulose and other plants. Unlike bioplastic manufacturing, traditional manufacturing of conventional plastic products utilizes non-renewable petroleum and natural gas resources. Their manufacturing processes are wasteful and not very environmentally-friendly. And while most plastics can be recycled, very few are. In fact, plastic is one of the fastest growing components of the general waste stream and one of the most expensive discarded materials for municipalities to manage.
Bioplastic Manufacturing at Urthpact
Traditional injection molding processes do not work very well for bioplastic manufacturing and making compostable, plant-based bioplastics. In order to develop an efficient, cost-effective means of bioplastic manufacturing , we had to rethink everything – from raw stock processing to mold-making to finishing.
We have spent a lot of time and effort closely examining various ways to develop processes for bioplastic manufacturing and utilize plastics made from plants, not petroleum. We discovered that bioplastics such as those produced here at UrthPact share many of the same properties of traditional plastics, just none of the environmentally-unfriendly ones. Bioplastic manufacturing can provide products with the same look, feel, and functionality of conventional petroleum-based plastics, but utilizing attractive, durable bioplastic that can be composted and safely converted into soil components within as little as three months.
Here at UrthPact, we’re committed to developing next-gen bioplastic technology and materials for bioplastic manufacturing to help consumer products companies produce better plastic products in a renewable, ecological way that doesn’t harm the environment.
To find out more about how UrthPact can help you make the change to eco-friendly bioplastics, contact us today.