Recent News and Updates
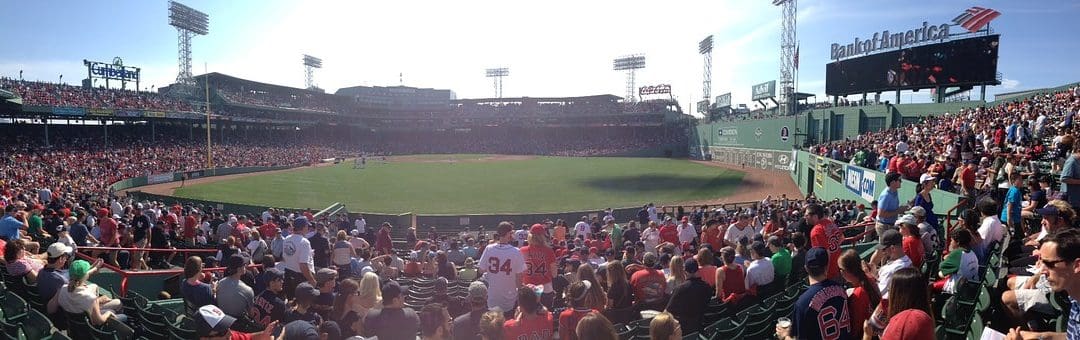
From Zero to Hero: Zero Waste Initiatives
Zero waste initiatives are gathering steam, especially, in large sporting venues and airports which historically have generated considerable solid waste from vendors and thousands of fans and travelers. Major ballparks such as Boston’s beloved Fenway Park and the Los Angeles Coliseum, as well as international airports such as Atlanta’s Hartsfield-Jackson are all getting on board with zero waste initiatives designed to drive down the cost of waste processing and removal as well as promote greener, more conscientious treatment of the environment.
Fenway Park, home of the Boston Red Sox, is the oldest ballpark in the country, but it’s also one of the most advanced when it comes to recycling and composting. Fenway Park is now a single-stream recycling facility, meaning all recyclable materials can be co-mingled, including plastic, cardboard, and paper – encouraging fans to recycle their food containers and programs instead of just tossing them in a trash can.
Even Atlanta’s Hartsfield-Jackson International Airport is getting in on the recycling action. As one of the busiest airports in the world, it was ripe for adopting an aggressive approach to recycling and began planning for a first-of-its-kind recycling and composting facility on airport grounds. While the project is still in the planning and proposal stage, the city is looking to have the program up and running by 2020.
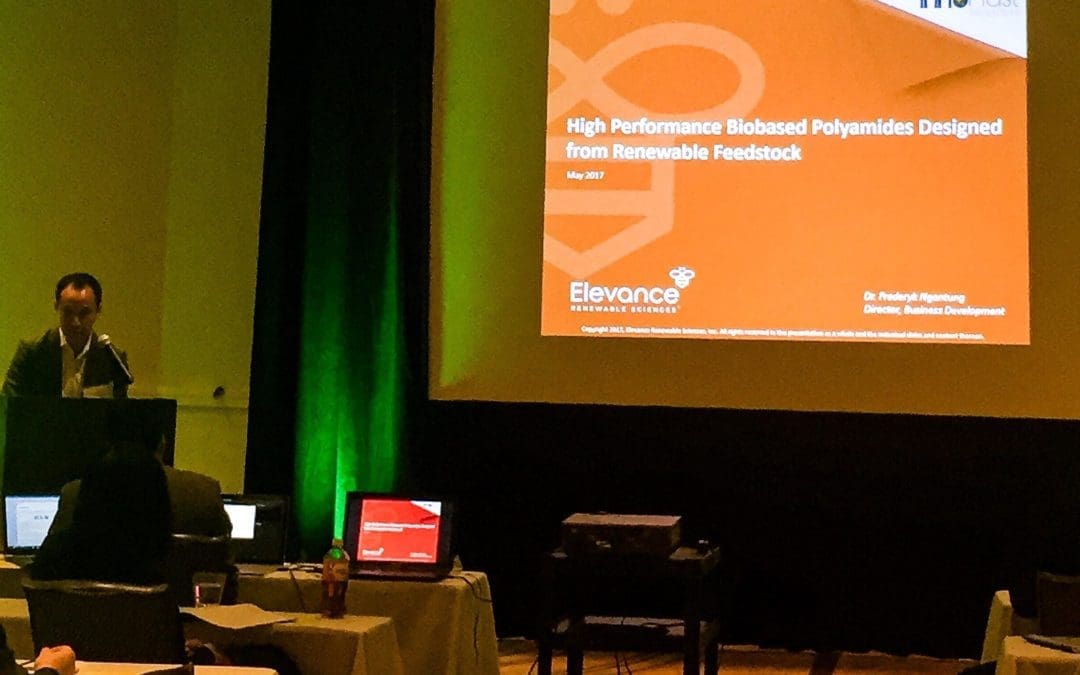
Insights and Innovations at Biobased Re-Revolution of Plastics
We got a chance to connect with UrthPact’s own VP of Technology, Derek Helmer, and VP of Operations, Mike Pousland, about their recent trip to Newark, NJ for the InnoPlast Solutions Conference, May 23-25th. The InnoPlast Solutions goal is to adopt a mission related to plastics, innovation, and business growth and select a team of technical and business savvy experts to educate participants. The conference offers solid networking opportunities as well for the plastic and bioplastic industry. The focus and theme of this year’s conference, BioBased Re-Revolution of Plastics, was to highlight the utilization of non-fossil raw materials that leads to preservation of petroleum resources and reduction of air/ land/ water pollution.
As far as the UrthPact team is concerned, this conference delivered a great value as it was full of participant engagement and packed full of information rich presentations showcasing topics related to the bio-industry.
Without a doubt, the biggest take-away was the strong drive on the part of attendees and presenters to replace petroleum as a feedstock for polymers before the Earth runs out of oil or oil prices become too high. Research has shown that solutions to this pressing problem will be found in developing bio-based replacements for existing polymers such as BioPE, BioPET, PEF, and PTF or finding new polymers that can replace existing materials such as PHA that do not source from oil.
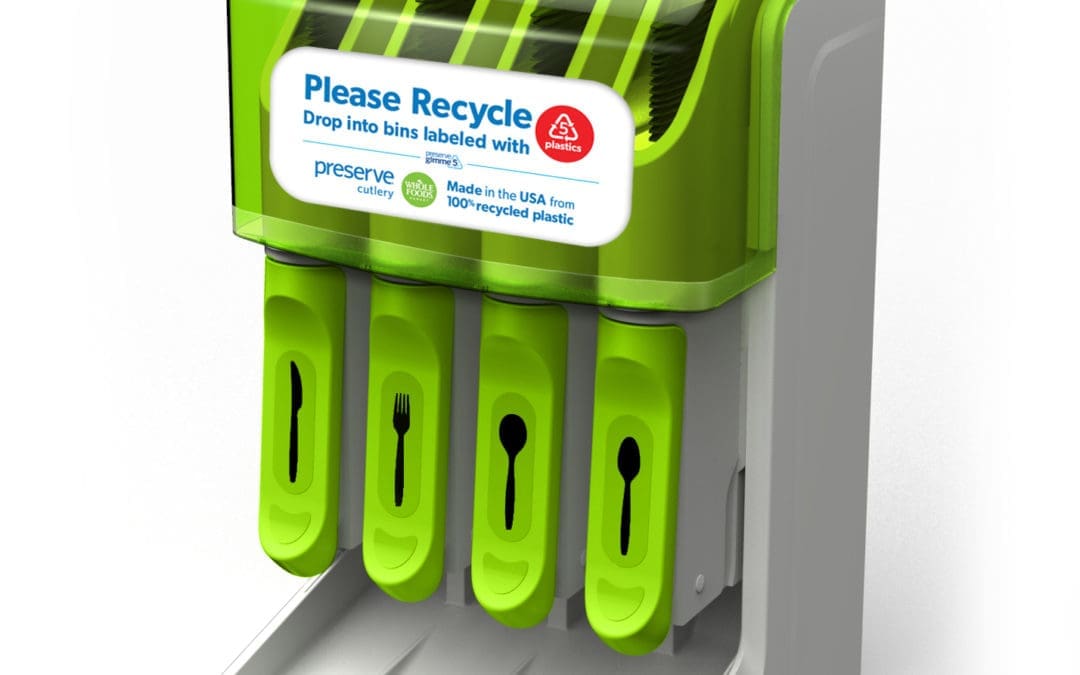
Urthpact is Now Manufacturing Single-use Recycled Flatware
Urthpact is excited to announce that we’re now manufacturing high-quality, single-use recyclable plastic flatware for food service suppliers, grocery stores, and other food services companies. This high-quality, fully recyclable plastic flatware will enable food service providers to provide their customers with environmentally-friendly products that will help create a more satisfying customer experience and build brand loyalty with environmentally-conscious consumers.
Waltham Massachusetts based consumer products company Preserve has tapped UrthPact to manufacture the single-use plastic cutlery and dispensers using 100% recycled polypropylene (#5) plastic collected through Preserve’s Gimme 5 plastic recycling program. The company recently exhibited its new line of earth-friendly food service products including the new UrthPact produced recycled cutlery and dispenser at the National Restaurant Association show.
It is exciting to be producing these sturdy and attractive recycled utensils right here in the USA using manufacturing facilities that have been certified by the global food safety organization AIB International to ensure the highest levels of quality.
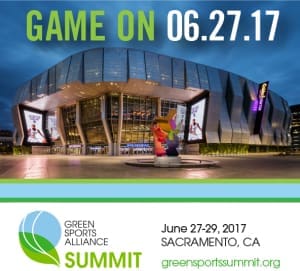
UrthPact Sponsors Green Sports Alliance Summit 2017
UrthPact is a proud sponsor of this year’s Green Sports Alliance Summit, June 27-29 at the LEED Platinum Golden 1 Center in Sacramento, California –home of the Sacramento Kings NBA basketball team. We’re excited to be a part of the growing movement to make a positive environmental and social impact on the sports industry and its fans.
The Green Sports Alliance will bring sports leaders together from 15 leagues, representing 14 countries at the Golden 1 Center, a venue that’s entirely powered by renewable energy. With a theme of PLAY GREENER™, the seventh annual Summit aims to accelerate fan engagement; educate youth on sustainability through sports; and leverage the $485 billion sports industry to tackle energy, waste, water, food, transportation, and other sustainability issues in sports.
Olympians Mary Harvey and Jill Savery, Hall of Famers Bill Walton and Peter “PT” Townend, NASCAR stars Joey McColm and Julia Landauer, and numerous other athletes who care about our world’s future will share the stage with Yankees VP Operations Doug Behar, Mercedes-Benz Stadium General Manager Scott Jenkins, Arizona State Athletic Director Ray Anderson, and other team executives who lead the way in greening sports venues.
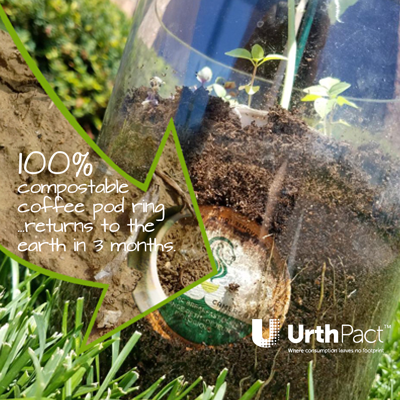
ICAW 2017: Biodegradable Plastic? Compostable Plastic? BioCompost? What’s the difference?
In honor of International Compost Awareness Week this week we’re going to focus on compostable plastic – what it is, what it can be used for, and how it can benefit the environment.
Because being “green” and “organic” are seen as positive attributes for a long list of products and services, these terms have been adopted by marketers and muddied to such an extent that it can be difficult to truly understand what really is earth-friendly. The term “compostable” falls into this category, so we’re going to help clarify things in this post.
Compostable plastic has been defined by ASTM International standards D6400 and D6868. These global standards require that for plastics to be labeled “compostable” they must biodegrade within a certain period of time and leave no toxic residue in the soil. Plastic that is compostable is a bioproduct manufactured from renewable resources such as plant-based materials.
Specifically, ASTM Standard D6400 covers plastics and products made from plastics that are designed to be composted in municipal and industrial aerobic composting facilities. This specification is intended to establish the requirements for labeling of materials and products, including packaging made from plastics, as “compostable in municipal and industrial composting facilities.”
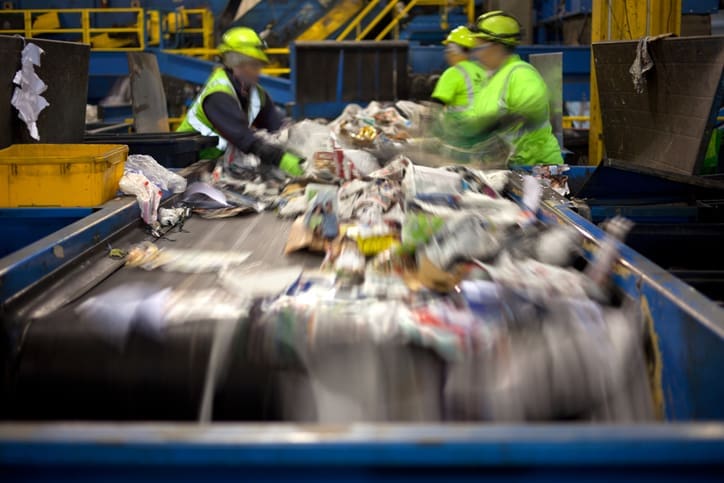
Plastic Makers Facing New Regulations Around Circular Economy
As recycling initiatives pick up steam nationwide and increasing numbers of states and communities embrace easier, more convenient recycling programs, legislatures are starting to consider more aggressive regulations around something called extender producer responsibility (EPR).
EPR is a fundamental element of a larger economic approach known as a circular economy. Essentially, a circular economy is an approach to manufacturing and recycling aimed at reducing wasting and avoiding pollution in two ways – through the use of biological nutrients which re-enter the biosphere to break down safely, and technical nutrients, which are high quality components that can be recaptured and re-used over and over again in the manufacturing process.
By extending producer responsibilities for their products and the materials used to make them, governments are mandating that companies assume end-of-lifecycle responsibility for what they use and how they use it. EPR systems and programs, such as the one now in place in California managed by the Department of Resources Recovery and Recycling, require manufacturers to fund and manage recycling and disposal programs for their products. In the United Kingdom, government regulations now require packaging manufacturers to ensure a certain proportion of their packaging is recovered and recycled.
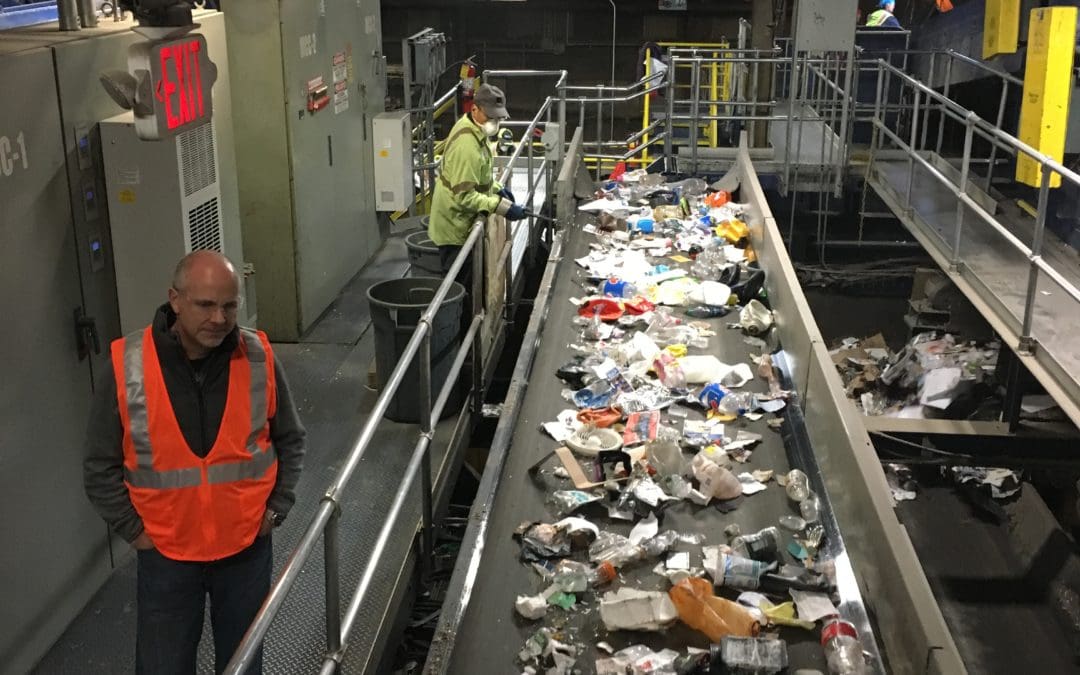
Reducing Landfill Waste with Innovative SEED Program
This month we’re spotlighting the Casella Waste Systems SEED™ (Sustainable Environmental and Economic Development) program. Our CEO Paul Boudreau and the UrthPact leadership team went to see Casella in action last November. Casella is serious about separating the 230,000 tons of glass, aluminum, paper, and plastic waste to ensure usable component sources for companies that want to use recycled materials in their manufacturing process. It is programs like Zero-Sort Recycling at CSC and UrthPact compostable plastic injection molding techniques that are working to change the course of our landfills.
It would be nice to think that all non-recyclable waste is going away sometime soon. The reality of the matter is that it is not. As a society, we will continue to be confronted by the need to dispose of a wide range of waste. However, companies like Casella and UrthPact are stepping up to address the challenge in a significant way by streamlining recycling to recapture as much waste material as possible and keep it in the manufacturing and consuming cycle. Instead of being relegated to wasteful, one-time consumption, materials used in manufacturing are kept in active use, not cast off to fill up landfills and incinerators. The way we see it, here at UrthPact, we’re helping communities and universities like Dartmouth reach their sustainability goals by making compostable bioplastic products while Casella helps on the disposal end with single stream recycling and commercial composting facilities.
For example, UrthPact team members saw how Casella’s Zero-Sort® Recycling solution simplifies the recycling process for consumers and business alike by allowing them to simply place all of their recyclable materials in one bin (single-stream recycling). This enables more materials to be recycled more frequently because it takes less effort and thought on the part of home- and business-owners who no longer have to sort and store recyclables separately, by category and type.
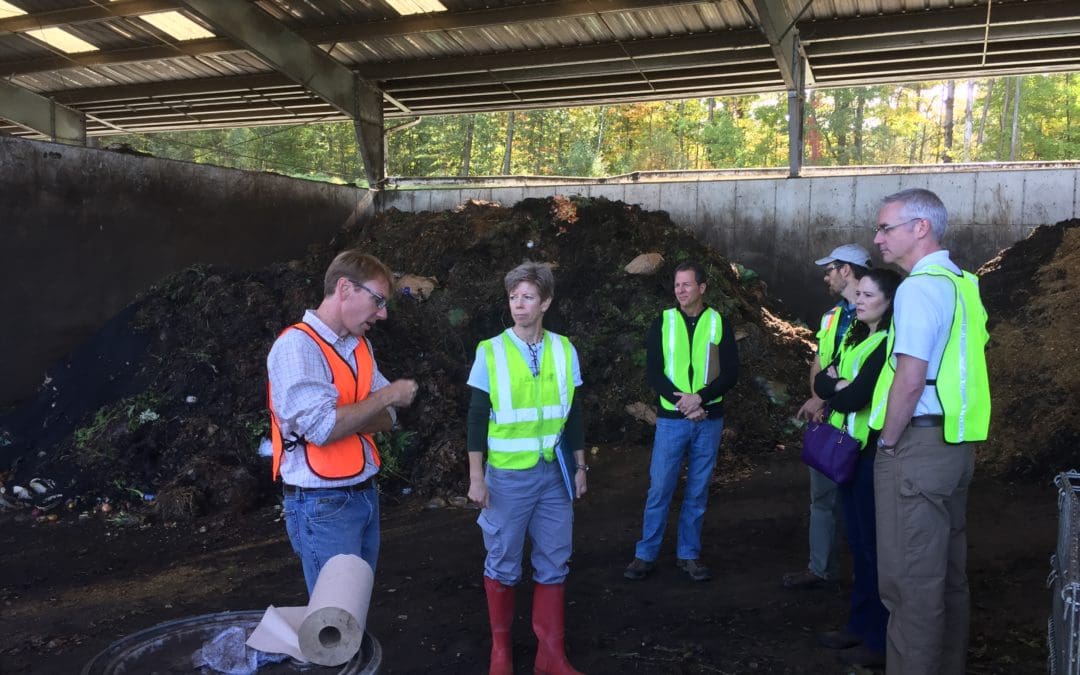
A Look at Home Composting in Winter
Last October, Urthpact CEO Paul Boudreau sent his leadership team to Green Mountain Compost in Vermont to get the inside view on the challenges that composters face and how to make our compostable plastic products even more eco-friendly.
Paul Boudreau and the UrthPact team were reminded of a few important facts about composting that they thought would be helpful to pass along. First and foremost is the fact that not all compostable materials breakdown easily. For products to be “certified compostable” they must:
- Break down completely into organic matter
- Break down 90% in 84 days.
- Be consumed by microorganisms in the compost at the same rate as natural materials such as leaves and food scraps
Our vegetable-derived plastics are compostable, but composting must occur in a commercial compost system that utilizes higher temperatures and a greater concentration of bacteria to do the work. They will not break down easily – at least not yet — in a simple backyard compost pile. Fortunately, commercial composting does work well for our retail-use, compostable plastic products.
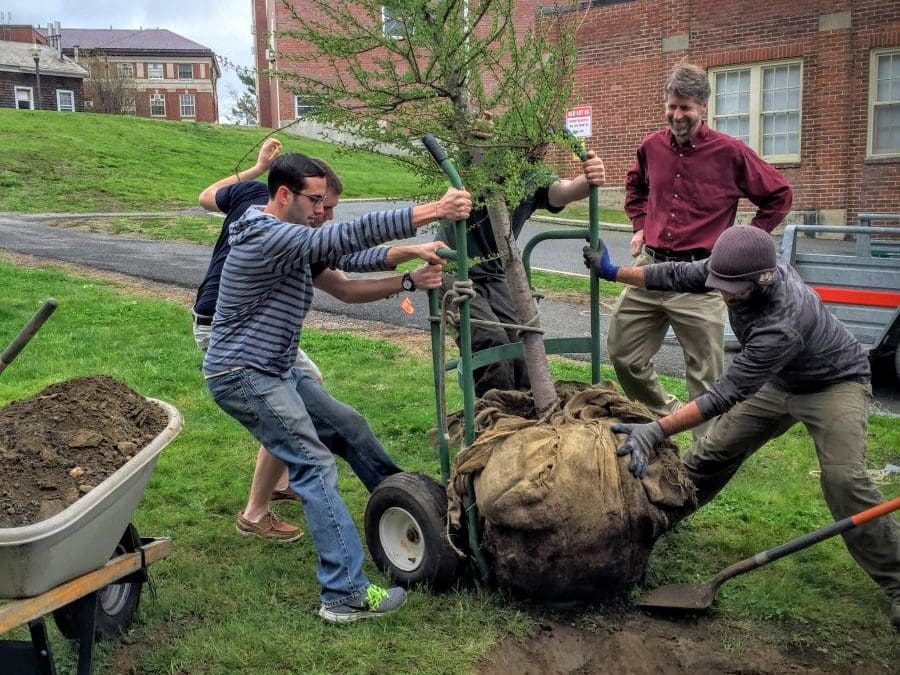
Spotlight on New Sustainability Initiatives
Here, at UrthPact we’re all about sustainability and developing compostable bioplastic products made from renewable feedstocks instead of non-renewable, petroleum-based resources.
In the course of promoting environmentally-friendly, plant-based plastic products, UrthPact CEO Paul Boudreau has witnessed the growing sustainability movement around the country and the world. In an effort to shine a brighter light on regional efforts to reduce the human impact on the environment, we’ll be highlighting various sustainability programs we are aware of , starting with the broad, pro-active approach being taken by UMass Amherst.
Sustainable UMASS: A University Striving to Practice What It Preaches
At UMass Amherst, students, faculty and university staff all have opportunities to not only learn about sustainability, but put what they learn into practice as well. UMass students can learn sustainability theory and practice in over 300 courses, 25 undergraduate majors, 15 graduate programs and undergraduate research experiences focused on sustainability. read more…
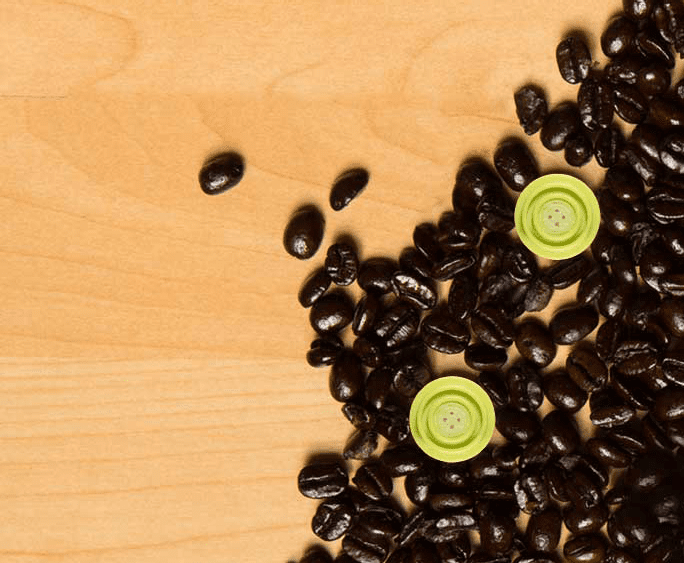
Adventures in Plastics with Paul Boudreau
Plastic is everywhere. It is almost impossible to pick up a product these days that does not have some amount of plastic in it. There’s a good reason for this, though – plastic is relatively inexpensive, durable, versatile, and attractive. It comes in a variety of compounds, formulations, textures, colors, and strengths. Plastics are used in virtually every industry and application, including healthcare, toys, electronics, transportation, packaging, clothing, furnishings, buildings, and others far too numerous to list here.
But plastic has its drawbacks, too.
Conventional plastics are made from non-renewable petroleum and natural gas resources. Their manufacturing processes are wasteful and not very environmentally-friendly. And while most plastics can be recycled, very few are. In fact, plastic is one of the fastest growing components of the general waste stream and one of the most expensive discarded materials to manage.